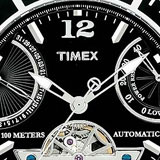

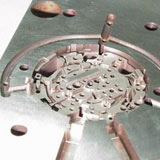
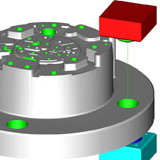
Time to change with PEPS Wire EDM
Based in Besançon (East of France), Fralsen is a company who specialise in the production of mechanical pieces for watches. Part of the Timex group, the main emphasis is the manufacture of business watches, but the company is also involved in the design of cutting tools and injection moulds.
Often working with tolerances of less than one micron (0.001mm), Fralsen recognised that cutting edge Wire EDM technology was essential to the future success of their manufacturing business. In this world of sharpness and precision, wire EDM technology enables the machine to cut intricate contours and internal corners with very small corner radii based on the wire diameter and spark gap. It becomes easy to cut square apertures without the need of splitting the mould or producing accurate pin holes in a plate after heat treatment. Support for unmanned or overnight machining is possible by leaving slugs attached while all of the preliminary cuts are taken. For example, taking all of the rough and finish cuts while leaving the tag in place and finally removing the tag and skimming the remaining area.
After a lengthy software evaluation, and a recommendation from Makino, PEPS Wire EDM was selected to drive the Agié Evolution 2 and a Makino PH2 wire EDM machines on the shopfloor.
A choice based on experience
Fralsen have over 20 years experience of Wire EDM technology and were previously using an old Mecanic CADCAM solution. Mr Larrandabure, workshop manager explains the reasons for upgrading their technology. "Wire EDM is a vital part of our operation and we were looking to save time for the 2 engineers in charge of the EDM machines. In fact, we were convinced that using the latest computer technology, we could not only improve our productivity but also make better use of the machine capabilities".
Mr Larrandabure continues, "Customer data is commonly supplied as 3D data so the software must be able to manage to read Parasolid and IGES files and extract the relevant EDM features. Whatever the quality of the model data, the software must know how to quickly generate the programs by removing the laborious tasks and helping the engineer with intelligent decisions. We want the engineers to concentrate on their job and not be constrained by the limitations imposed by the software."
With an existing CADCAM system already in place, it was imperative that the new solution was operational immediately with no down-turn in productivity. The selection of PEPS was based on real programming of live jobs and the guarantee of highly tuned post processors. The advanced postprocessors aren’t just limited to the use of generic G and M codes - special posts are easily configured to suit different machine models and configurations.
The implementation of technologies
The implementation of the cutting technology within PEPS was a major focus of the training course. The standard technology provided is easily adapted through intuitive dialogs to suit the specific requirements of the customer. The user is able to modify standard parameters such as a Surface Finish and add his own custom technology if required. Makino developed technology parameters are, however, integrated as standard therefore all the experience and know how of the company are available to the engineer. This means that user technology customisation is generally not required. Mr Larrandabure comments: "For us it is a real relief, we are able to program jobs much quicker than before and we are no longer waiting for programs to be completed. The use of PEPS means that a program which may have taken half a day to complete with our old system is now available in half an hour."
After a week of training, the 2 EDM operators gave up working with their former system and PEPS became the software of choice.
About The Company:
Name: Fralsen
Benefits Achieved:
- Can now import more data formats from all major CAD vendors
- Upto 70% reduction in programming time
- Makino developed technology inside the Wire EDM software
"The use of PEPS means that a program which may have taken half a day to complete with our old system is now available in half an hour.”
Mr Larrandabure