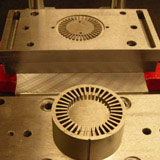
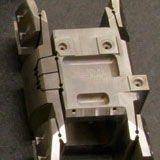
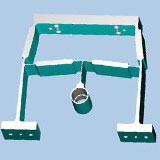

PEPS Wire EDM - Out Of This World
Founded in 1996, Next Intent (California, USA), have developed a reputation as experts in subcontract manufacturing with a machine shop configured to handle both prototype work and production machining for a wide variety of industry sectors including aerospace, military and scientific fields.
A prestigious client list including ATK, Lockheed Martin, Raytheon, Superconductor Technologies and JPL (Jet Propulsion Laboratory) have led to Next Intent being involved is a number of sophisticated projects including the NASA Mars Phoenix Lander as well as the Mars Rovers where components for the Rover wheels, suspension arms, fittings and cameras were manufactured.
The 32 employee company runs a policy of investing in the latest CADCAM and machine tool technology to ensure they remain competitive in the current climate. This innovative development strategy has seen the introduction of PEPS Wire as the primary programming solution for wire EDM and the commissioning of three Sodick wire EDM machines. In 2003, Next Intent purchased their first Sodick AQ750L and in 2005, the Sodick AQ325l was added including a KC1 hole drill to support the EDM capacity. Finally in 2007, the Sodick AQ300l 5 axis (6 axis optional) was purchased to increase productivity on multi-axis indexing components.
Next Intent have over 250 years of combined experience for machining all types of materials including Stainless Steel, Nitronic, Invar, Vimvar, Aluminum, Titanium, Inconel, Bronze, Copper, Macor, PET (Ertalyte), PPS, PBS, Ultem, Acetal (Delrin), UHMW, Turcite, Vespel, PEEK, Celezole, and Nylons to tolerances within 0.0002". "This is a major advantage" explains Chris Baker, Manufacturing Manager. "We have knowledge of our customer's needs and have become a leader in our industry by developing partnerships with our customers to help reduce overall costs, improving quality and meeting delivery requirements."
Matt Redman, manufacturing process engineer with over 19 years experience working in the aerospace industry explains how the introduction of PEPS and the Sodick EDM machines have revolutionised their manufacturing processes. "Although I have been involved in manufacturing for a long time, I had no prior experience with the programming or operation of wire EDM machines prior to Next Intent purchasing our first Sodick. We ran a benchmark test comparing 3 leading CADCAM systems and PEPS ran-out the clear winner because of integrated Sodick machine technology, and the ability to extract geometry from customer solid models".
The benefits of PEPS Wire EDM were evident on a recent project for Lawarance Livermore National Laboratory where Next Intent manufactured and delivered on time 1500+ actuator assemblies complete from project planning through clean room assembly and testing. A key component in the assembly required delicate wire EDM operations that involved rotating the part to complete all of the details without the need for additional set-ups. With the addition of the Sodick AQ300l rotary axis and supporting software technology within PEPS, Next Intent was able to successfully run parts “lights out” increasing production time and reducing overall cycle times by more than 50%.
Commenting on the support and training, Matt continues, "After a 3 day basic training class I was able to use the system confidently and could contribute productively. The transition to more advanced options has been easy and four years later I continue to learn and continue to use the latest advanced developments that PEPS provides. The customer service and technical support has been great - any questions or challenges I have had are handled promptly with a knowledgeable response."
Concluding, Chris Baker, Manufacturing Manager explains how PEPS has exceeded all expectations. "The software has always delivered and having the ability to enhance the system with advanced modules has made it more cost effective. The ability to start basic and easily enable advanced modules as you learn the system, is a benefit to any job shop".
About The Company:
Name: Next Intent
Web: www.nextintent.com
Benefits Achieved:
- Support for Sodick AQ300I rotary axis
- Up to 50% reduction in programming time
- Highly-tuned machine specific post processors
"We ran a benchmark test comparing 3 leading CADCAM systems and PEPS ran-out the clear winner because of integrated Sodick machine technology.”
Matt Redman