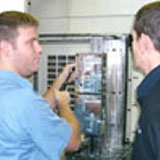
PEPS Milling with Custom Fluidpower
Custom Fluidpower Pty Ltd, based in Australia, utilises the latest in Cartridge Valve Technology including SUN Hydraulics and Waterman Hydraulics to design and manufacture state-of-the-art hydraulic manifolds covering industrial, mobile, agricultural, marine and aerospace applications. Until recently, however, they were still programming their Okuma horizontal machining centre using an internally created database of machine code for individual features. Bob Nolan, Manifold Manager commented; "All features were hand-written in G-code, which was time-consuming when features changed. Also, we had no way to simulate the cutting cycle. This process required a great deal of technical expertise."
They decided to investigate CAD/CAM solutions, but no single system offered the end-to-end solution they desired. After speaking with Camtek Pacific they decided to purchase PEPS Milling, with Camtek Pacific developing a parametric manifold generation application - CAM Expert - using the PEPS open structure and customisation facilities. Functions and interfaces available include creating user-commands and algorithms, interface dialogue boxes and database accessing.
Once PEPS was installed and configured in January 2004 several benefits became immediately apparent. Machine efficiency increased by 25% to 80% through optimised code routines, which yielded greater capacity. Denver Pollock, Engineer, added; "The most recent manifolds we produced were completed in 3.5 hours as opposed to the usual 6."
Said Bob; "The main advantage is the capability to generate complete NC program to machine a manifold directly from the design data practically eliminating human factor. The reliable NC program ready to go for unmanned NC machining is generated in minutes instead of hours." Denver added; "I am a lot more confident using PEPS programs over previous when we set up and prove out our first blocks. It is always correct once we have proven features."
Through PEPS and the integrated parametric module written by Camtek Pacific tool changes were reduced by 75%, which also constituted to a half hour saving on an average manifold. For every parametric feature CAM Expert has rules for its machining, configured by the company's personnel. CAM Expert uses these rules and the tool cut database to resolve all required machining operations to produce all features and to cut the manifold.
Bob concluded, "PEPS has been an important ingredient in gaining efficiency within our manufacturing facility. Our main objective with PEPS was to produce a superior product where we could guarantee quality and consistency of our products. This alone has made us more efficient and substantially reduced our manufacturing costs. When you get this right all the other issues seem to fall into place. In conjunction with our customized design software, PEPS has been the nucleus for our success in reaching our objective."
About The Company:
Name:Custom Fluidpower LtdWeb:www.custom.com.au
Benefits Achieved:
- 25% increase in overall machine efficiency
- Manifold cutting reduced by over 40%
- Excellent local support from an international software vendor
- Can now simulate part cutting before running job on the machine
- Tool changes decreased by 75% due to knowledge base and no requirement for operation sequencing
- Once a part has been proven quality is guaranteed
- Future outsourcing plans based around PEPS NC code
- Open software architecture allowed reseller to build custom module
Comments:
"The best aspect of PEPS is its ability to be customized to suit our needs."
Bob Nolan
Manifold Manager