
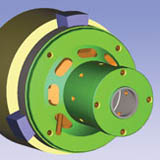
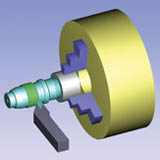
PEPS Turning
Advanced CADCAM Software Solutions For The Manufacturing Industry
PEPS Turning is a leading CAD/CAM system that provides a practical and intuitive solution for the offline programming of Turning machine tools, from simple 2-axis lathes through to turning centres with live tooling, B, C and Y axes, and multiple spindles. PEPS Turning is used in thousands of product manufacturing, precision engineering and tool making companies around the globe.
Features at a glance:
- Intuitive graphical user interface
- Extensive range of CAD interfaces; both for import and export
- Comprehensive machine and postprocessor database
- Selectable machine setting; including turret configuration, tool change position, etc.
- Extensive range of roughing, semi-finishing and finishing strategies
- Profiling of simple or complex geometric boundaries with cutter radius compensation
- Standard hole cycle functions; including drilling, tapping and boring
- Threading cycles, plunge, flank feed, zigzag and tapered
- Grooving routines, simple plunging or allows machining of predefined part
- User configurable and expandable Tool and Material database
- Fully customisable solid visualisation of machining sequence; including tool shape
- Machinable fonts with user definable style, size, shear angle; inline or around an arc
- Calculation of cycle time for complete part
Comprehensive machine database. PEPS Turning contains a comprehensive database of Turning machines from a large number of leading Machine Tool manufacturers; including Acramatic, EltroPilot, Fagor, Fanuc, GE, Num, Okuma OSP, Philips, Siemens and Traub.
Full range of machining cycles. PEPS Turning offers many easy to apply interactive machining cycles for roughing, semi-finishing, finishing, grooving, drilling, tapping, threading and boring; as well as turning and facing operations, including shapes with undercuts. Various canned cycles, sub routines and work offsets are supported. End, side and developed working with driven tooling is also supported.
Comprehensive tool and material database. PEPS Turning has a fully integrated tool management database. Tools and tool holders are stored with all the relevant data associated to material types and cutting conditions. Default programming styles can be set up so that accurate information is automatically returned to the programmer; such as feed and speed information. The tool database can be intuitively interrogated using standard searching, ordering, grouping and filtering functionality; also it can be expanded by importing tool information from external sources.
Toolpath verification and simulation. Once programmed, the job can be simulated in realistic rendered solids. PEPS Turning automatically checks the tool and the holder against the model and fixturing and provides a warning when there is going to be a collision, both graphically and via on-screen warning messages. Graphical verification of the completed toolpaths shows the sequence of operations and the surface finish. The cut part can be compared with the original model, to ensure that the part has been completely finished. Using visualisation helps to make sure the job is made right first time.
Configurable postprocessors. An extensive library of advanced postprocessors is available to suit most machine tools and all postprocessors are fully configurable to suit individual requirements; they aren't just limited to the use of generic G and M codes. Canned cycles for roughing and finishing, drilling cycles, subroutines to reduce program length and tool length compensation all combine to produce reliable NC code which is easy to use on the shop floor.